Porcelain Commemorative Mickey Mouse Insulators
By Jason Townsend
Reprinted from "Crown Jewels of the Wire", March 2005, page 18
I've been collecting porcelain insulators for the last four years. The first
swap meet I attended was at the home of John and Carol McDougald while they were
still living in St. Charles, Illinois. After that meet, I was immediately bitten
by the collecting bug, and since then I've wondered about how difficult it would
be to produce a commemorative of my own. How much would it cost? Where would I
go to have a mold produced? How long would it take to manufacture once I had the
molds? So many questions with too few answers!
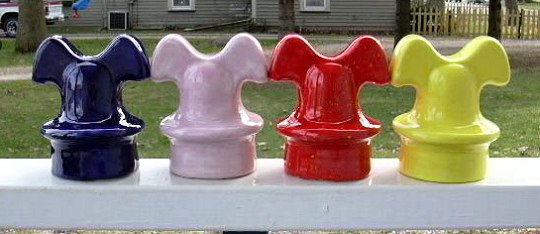
After speaking with Jim Crandall about my idea, I was encouraged to the point
where I decided to pursue my idea, and get this process rolling. I spoke with
Dudley Ellis at the Mid-Ohio show last November, and he saw no problem with what
I wanted to do. After speaking with the other board members of the NIA, I was
informed that my idea would be OK'd by the NIA if I were to clearly mark the
pieces in such a way that everyone would know they were commemoratives.
I looked on the Internet, and finally found a company in the Chicago area
that could produce the molds for me at a reasonable cost, and with a fast
turnaround time. My next step was in locating all of the supplies that I needed
to produce the pieces. My initial investment was climbing swiftly! Between
the molds (four of them), the cleaning screen, tools, pa sent to the kiln
to be fired for up to 12 hours. Once fired, each piece is hand painted three
times, and sent back for final firing in the kiln for up to 8 hours. Paying to
kiln dry them, shipment to the kiln operator, paint, brushes, and other
miscellaneous items, the price adds up very quickly! Not to mention the nearly 5
hours of time that it takes to produce each individual piece!
After much trial and error, I believe I have this process down to a science.
They will be available for sale at the show in Wheaton, IL on April 2, 2005.
Each piece will cost $25.
A special thanks to people who have helped me over the years: John and Carol
McDougald, Tom Nugent, Denley Bryson, Jim Crandall, Ken Willick, arid too many
others to mention here.
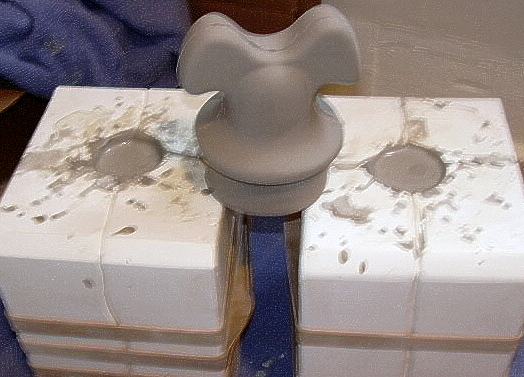
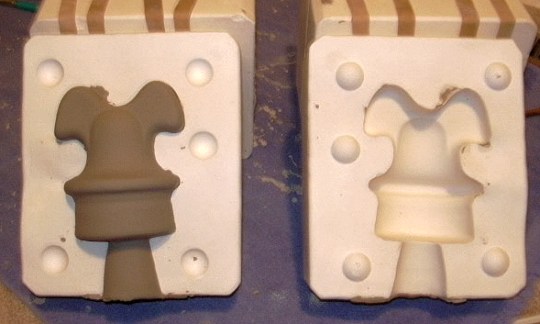
The molds are filled with the slip, and they need to stand for 30 minutes
before dumping the slip from the mold. Then, it stands for 3 - 4 hours before
opening the mold. Once the mold is open, each piece needs to dry for up to three
days, depending on humidity levels.
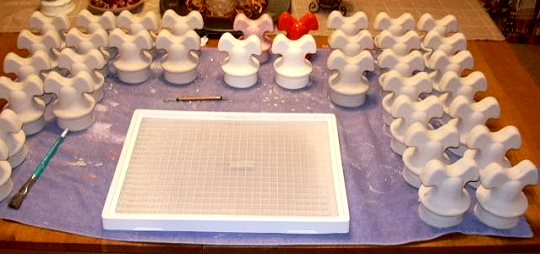
At this point, each piece needs to be individually cleaned, sanded, sponged
smooth and bases leveled with the screen (in the foreground). Then, they are
sent to the kiln to be fired for up to 12 hours. Once fired, each piece is hand
painted three times, and sent back for final firing in the kiln for up to 8
hours.
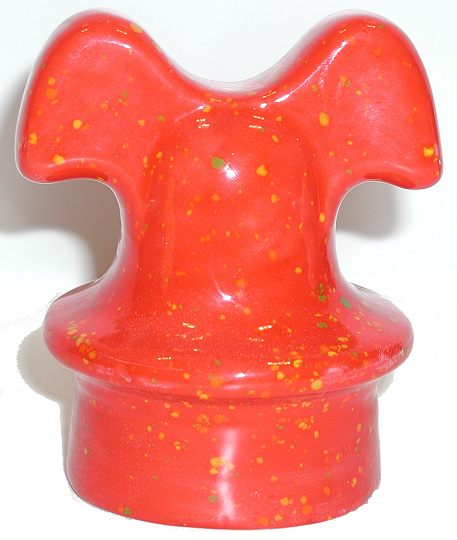
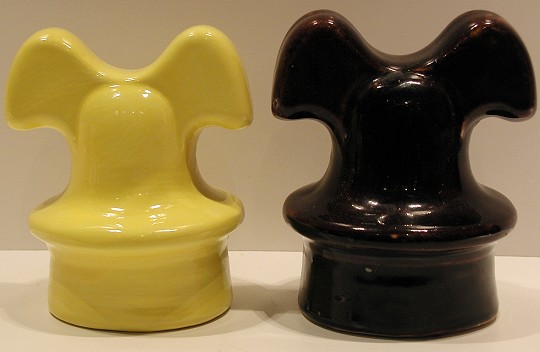
Shown above are the colors available -- Cobalt blue, Pink, Yellow and Firecracker red.
The yellow is shown next to an actual U 395 for size comparison.
Paid Advertisement by Jason Townsend.
|